Production Assistant Line Leader
Post :
Production Assistant Line Leader
Time :
full time
Salary :
market competitive
No. of vacancy :
05
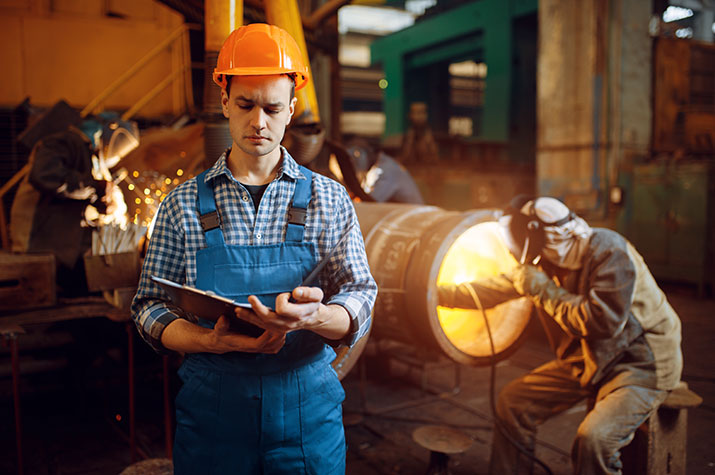
1. Set up the workers data and data of key position and special position staff.
2. Encourage staff to follow the rules of the company. manage teams to maintain employee daily work evaluation data and monthly special post performance appraisal data as well as weekly performance appraisal data for teams.
3. Create a manpower demand list for each line team, as well as a selection and training strategy based on the monthly production plan for Production Line Engineer and Assistant Production Line Engineer.
4. Work with Industrial Engineer to increase the process technology, line balance rate, and standard working hour utilization rate. Supervise teams in inventory of material and implement actions to decrease loss caused by the production department.
5. Direct the teams in putting the Process Department’s and Quality Department’s measures and action plans into action in order to increase yield.
6. Check the “Process confirmation sheet before production” and the “First article checklist” to ensure the quality and quantity of 4M1E (man, machine, material, method, and environment) before production.
7. Instruct teams to adhere to SOPs, and IPQC audits based on TOP3 abnormalities, assign improvement measures and action plans, and monitor each team’s execution.
8. Participate in production planning based on each line’s capacity. Make recommendations for production scheduling, attendance management, and overtime pay. Increase the process technology, line balance rate, and standard working hour utilization rate in collaboration with the Process Engineer.
9. Manage teams to obtain fewer extra material, count inventory materials, and create daily and additional material inventory records. For the production department, devise and implement material loss prevention
Graduation
Electrical/Electronic/Industrial Electronics